Polyisocyanurate Insulation Helps with Code Compliance, Energy Savings, and Earning Financial Perks.
Providing advanced thermal protection for the structures in which we live, work, and play is proving to be even more crucial than we ever considered. According to a 2023 article on Euronews, new research suggests that reaching net zero emissions could prolong people’s lives significantly, and that properly insulated walls help to limit indoor air pollution that negatively impacts the health of occupants inside.
Occupant health is priority number one. But how can builders use innovative insulation solutions to save on costs, build more efficiently, and meet the evolving energy codes designed to create a more sustainable built environment?
Polyisocyanurate insulation, renowned for its closed-cell composition, serves as a linchpin in bolstering energy efficiency for residential, multi-family, and commercial buildings. Its rigid form with closely bonded cells not only acts as an air barrier but also provides moisture resistance, which is critical in keeping internal structural components and occupants healthy. When combined with integrated control layers and a structural layer, the material crosses into what can only be categorized as the future of building science.
Proven Polyiso Performance
Weatherization systems, especially those incorporating closed-cell polyiso insulation such as OX-IS panels, have proven to be instrumental in optimizing energy efficiency and indoor comfort. These types of systems eliminate thermal bridging in both wood and metal wall studs, preventing the movement of heat and energy through the structure. This is especially vital during the peak of summer or the frigid depths of winter when temperatures are at an extreme.
Weatherization systems that utilize polyiso insulation provide much higher R-values compared to alternative products such as spray foam, XPS foam, or other open-cell insulation solutions. In fact, OX-IS is offered in three thicknesses ranging from 0.50² to 1.70² and provide thermal R-values of 3, 6, and 10.
OX-IS fortifies the entire wall system when properly taped, seamed, and flashed. By featuring an integrated structural layer along with air and water barriers, OX-IS eliminates the need to make multiple trips around a structure to complete the installation. Once installed, an OX-IS wall is a tighter wall. This leads to a better blower door score, enhancing HVAC system performance and reducing long-term energy costs.
Affordably Meet Stringent Energy Codes
Structural continuous insulation wall panels allow builders to affordably tackle code changes and meet the most current IECC insulation requirements. These weatherization systems also help ease specification planning for project teams looking to achieve ENERGY STAR® or the requirements for the Department of Energy’s Zero Energy Ready Home (ZERH) standards.
Where should builders look to get up to speed on what’s expected of them with regard to insulation and a building’s thermal performance?
Start with International Energy Conservation Code section R402.1.2, which is dedicated to a building’s thermal envelope. Understanding the options available to a builder, including different continuous insulation thicknesses and options for R-values, helps to ensure compliance with the latest requirements.
Adhering to these code standards through the implementation of all-in-one weatherization solutions can help builders earn significant money back for building sustainably through the 45L tax credit program, applicable to both residential and multi-family builders.
In particular, builders of single family homes that meet the ENERGY STAR Certified Homes V3.1 (moving to V3.2 in 2025)
program’s 2021 IECC prescriptive envelope standards are eligible for a federal tax credit of $2,500 per home.
On a parallel path, builders who adhere to the ZERH program can earn up to $5,000 back in tax credits per build.
In addition, builders should maintain cognizance of local and regional rebates extended by utility providers, which may offer substantial cash incentives contingent upon meeting these ENERGY STAR standards or achieving a high HERS score with significant Kilowatthour (KwH) savings. In these instances, adding a layer of continuous insulation to exterior walls will improve the performance of the home and translate to a rebate check with a bigger number on it. In an era of rising material and labor costs, these financial returns can impact a builder’s bottom line.
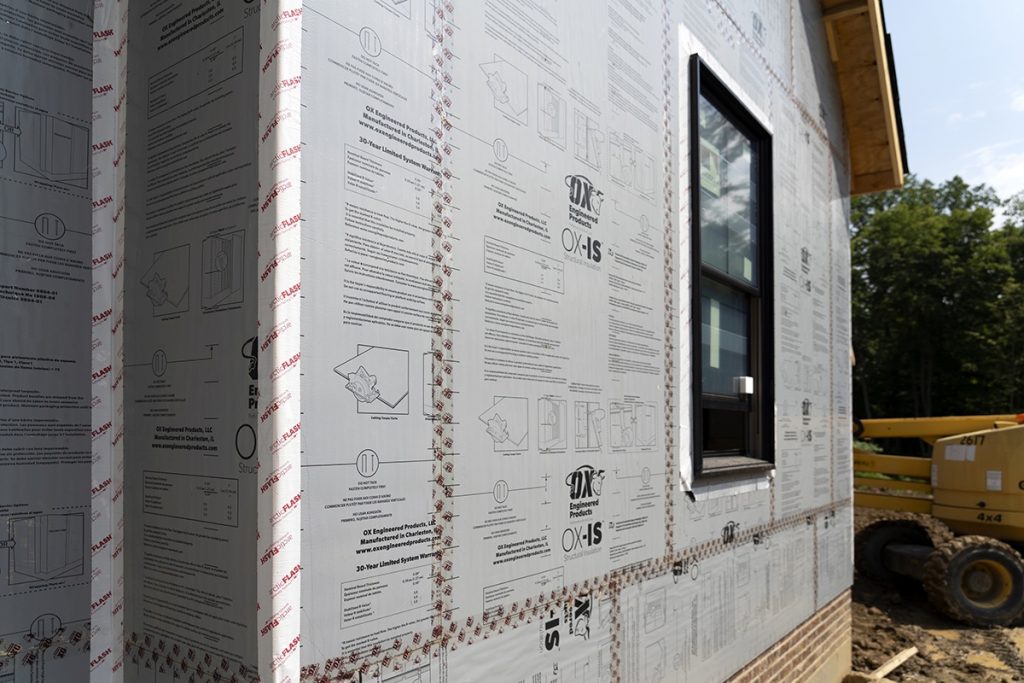
Sealing the Deal with Proper Installation
In the long term, the benefits of incorporating polyiso insulation and weatherization systems into a construction project are substantial. By eliminating thermal bridging, the building’s thermal envelope is fortified, reducing the load on heating and cooling systems. This translates to significant energy cost savings for owners. Not only do owners save, but builders can stick with 2×4 stud construction and still achieve code compliance without having to switch to a heavier, more expensive 2×6 wall. Finally, builders stand to gain financially through various rebate programs such as the federal 45L tax credit and local incentives tied to energy efficiency certifications and HERS ratings.
The adoption of polyiso insulation and weatherization systems represents a step in the right direction toward achieving the most energy-efficient, sustainable building practices. With its impressive performance attributes and compatibility with evolving industry standards, polyiso is poised to play a central role in the construction landscape of the future.
The post The Polyiso Promise first appeared on OX Engineered Products.